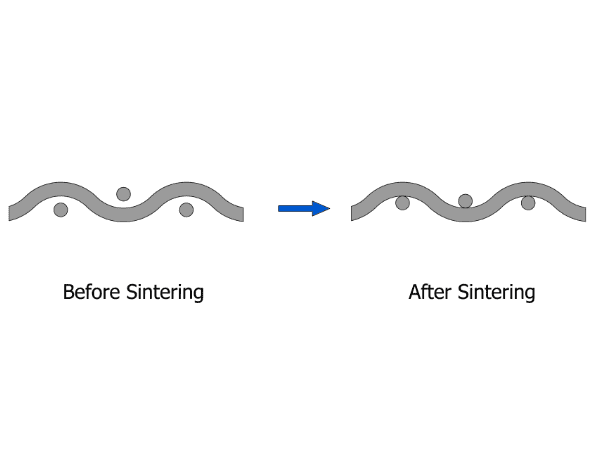
Wire mesh construction comparison
It is a process of metal material processing. The adjacent wires partially melt and merge with each other under certain pressure and temperature (lower than melt point) with time.
The microscopic phenomenon is atom immigration and settlement. After cooling the wires connect with each and the wire mesh or multi-layer wire mesh become a whole mesh plate.
Wire mesh construction comparison
Thickness comparison
The wire mesh is woven by looms, which interconnect the warp and weft wire with knuckles. There are apertures between warp and weft wire, thus the aperture is a loose part with changeable aperture size and the wire is subject to migration and shedding at the edge of the mesh. The wires merge with each other after sintering. Sintered mesh eliminates the possibility of migration and shedding, and makes the aperture size fixed.
By sintering multi-layer wire mesh, the sintered mesh laminates give the filtration layer good support and protection. So it can be better used for liquid or gas filtration.
For example, the 2 micron dutch weave wire mesh is only 0.08 mm in thickness, even thinner than a sheet of A4 paper. It is too fragile to work with any filtration task. After sintering protection and support layer, it forms the standard five-layer sintered mesh. The filtration rating is still 2 micron, but the thickness change to 1.7 mm. Obviously sintered dutch weave wire mesh construction is more stable than before.
Sintered mesh products mechanical properties significantly depend on the impurity concentration, grain size, and sintered density.
We can test products property by various quality standards as following:
Hardness | The hardness of the product is measured according to ISO 3878 and ISO 4507 |
---|---|
Sintered Density | The aperture ratio and the density of the sintered mesh are determined according to ISO 2738 |
Tensile Test | According to ISO 2740 |
Bend Test | The bending strength of the product is determined according to ISO 3995 |
Fatigue Test | According to ISO 3928 |
Microstructure Test | Conduct a metallographic analysis using optical microscopes and appropriate image software. |
Un-Notched Impact Test | According to ISO 5754 |